Turbine Monorail
My first design project out of college was to create a monorail system that could combine the sand blasting and non-destructive examination (NDE) inspection of incoming steam turbine diaphragms into one. Sand blasting and NDE are standard processes for steam turbine maintenance.
The initial design in SolidWorks.
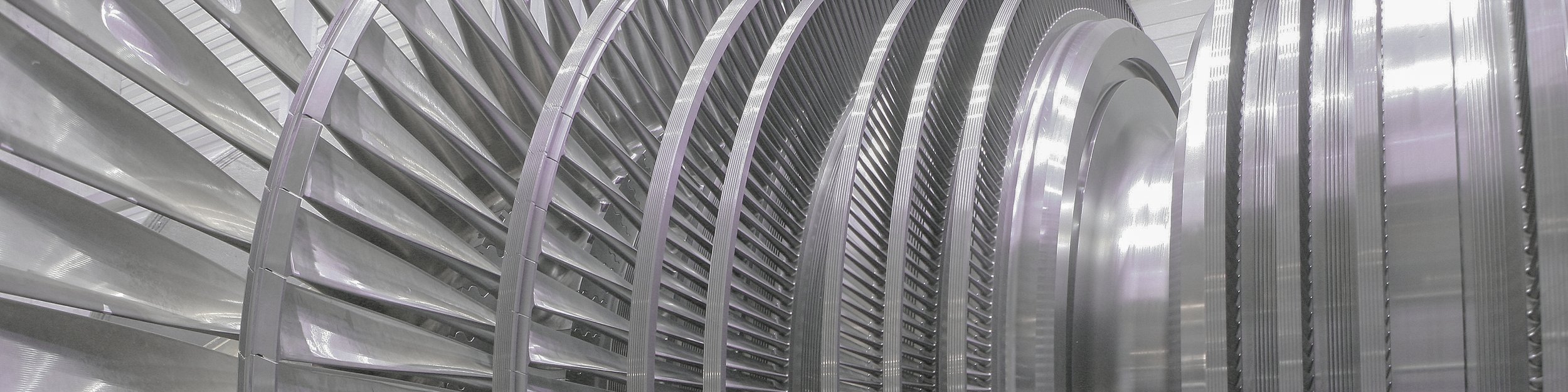
Design Constraints:
Schedule: 6 Weeks
Closed-loop system.
4-ton (8,000 lb) capacity per beam.
Monorail must be adjustable so it can be leveled if there’s an uneven floor.
$50,000 USD budget.
All components must fit inside a conex container so it can be transported.
Process
Turbine diaphragms are be loaded on this right side and then they’re pushed counterclockwise to the sand blasting booth. The diaphragms are sand blasted to remove incoming scale and debris.
Once they’re sand blasted, they are pushed to the NDE area on the opposing side. This is where they’re inspected for cracks and imperfections.
Once the inspection is completed, the diaphragms can be removed and sent to the dimensional inspection area.
Dimensional Inspection
The diaphragms are transported via crane to the dimensional inspection area and then they’re dimensionally inspected using a CMM FARO Quantum Arm which has accuracy down to the thousandths of an inch.
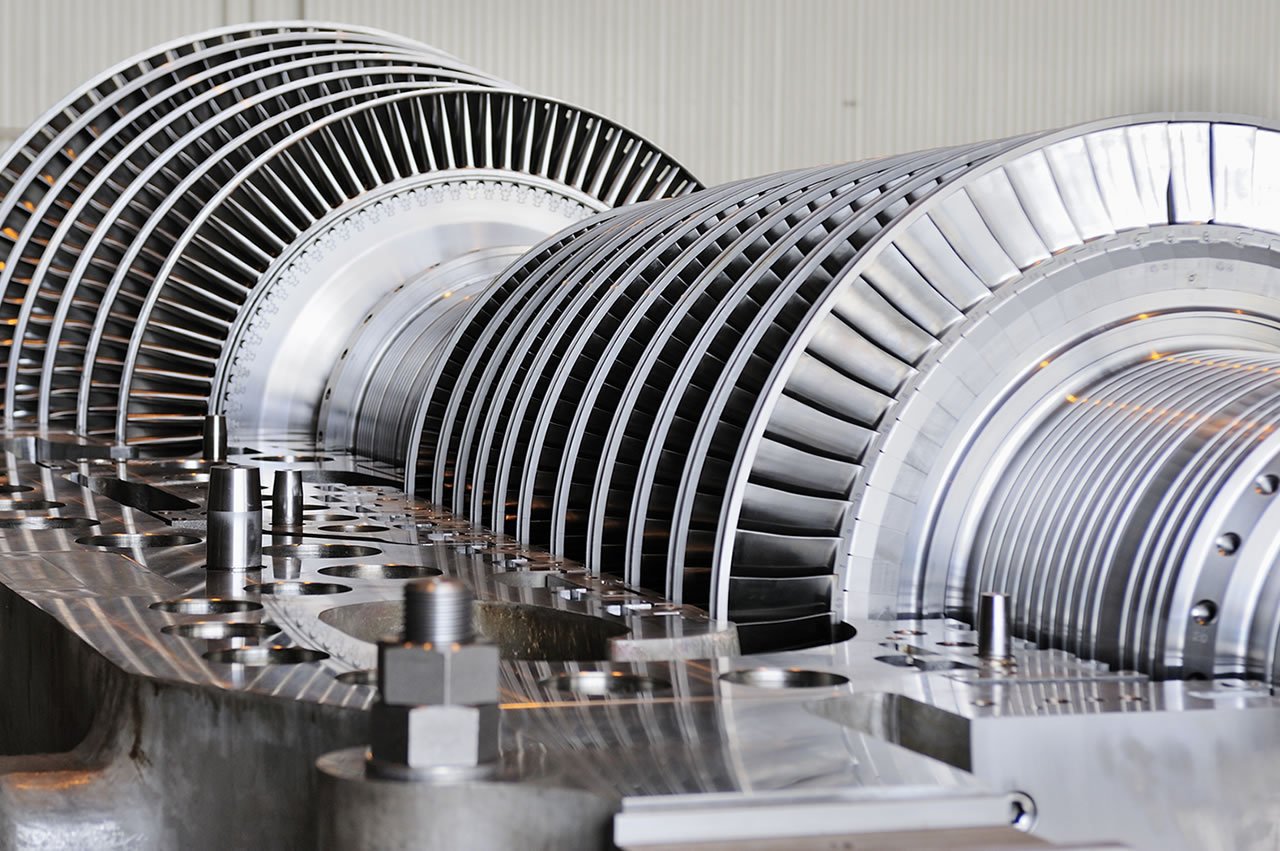
Adjustable Mounts
Close-up of the adjustable rail mounts using Grade 8 all-thread and Grade 8 Zinc Yellow Chromate Plated Steel Hex Nuts which are 25% higher than medium-strength nuts.
Final Assembly
The monorail improved inspection times significantly and was a huge success. The best part is that it’s still in use today after 9 years!